Posted 5th August 2008 | 1 Comment
It’s 14 a night, every night, as super depot hits targets
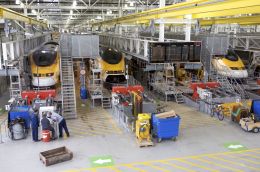
Eurostars line up in the state-of-the-art depot.
On 14 November last year Eurostar’s new £402 million train engineering centre in east London went fully operational, as services started on the new high-speed line – HS1 – running between St Pancras International, Paris and Brussels.
Since then the state-of-the-art centre, which was built on old marshalling yards and is more than a quarter of a mile long, has been breaking records in ensuring the availability of enough Eurostar trains to run the new services.
Railnews chief reporter David Ewart and photographer Duncan Phillips were invited behind the scenes to see the giant depot in operation.
IN maintaining 14 Eurostar trains every night of the year since opening last November, Euro-star’s Temple Mills Engineering Centre in east London has consistently beaten its tough 96 per cent train availability target, often hitting 100 per cent.
“We’ve never failed to provide a train,” says head of engineering production David Bailey, who is clearly justly proud of his team’s achievement.
The £400 million maintenance depot replaced the far less convenient North Pole in west London. With direct access to the HS1 route from Stratford International and within 10 minutes of St Pancras International, Temple Mills can accommodate eight quarter-mile-long Eurostars at a time.
No longer having to divide trains saves around two hours on each service, which ranges from three-day light inspections and servicing to 36-monthly heavy maintenance.
Around 342 highly trained members of Eurostar’s workforce transferred to Temple Mills, with only two leaving the company – a clear measure of the team’s loyalty and job satisfaction.
In the depot’s nerve centre operations controller Malcolm Stone signals an incoming train from St Pancras International. Despite passing through the sophisticated bi-directional carriage washer, the Eurostar's front end still appears travel-stained.
“The problem is 186mph collisions with myriads of insects which become embedded in the paintwork,” explains technical training assessor Peter de Lacey, a Eurostar man for the past five years.
“Hopefully, during mid-life refurbishment, improved technology will be able to provide a more resilient paint finish, but for now we have to revert to good old ‘hand bashing’ to clean a train for any special occasions.”
More serious are 186mph collisions with wild boar, which can require a replacement nose cone. Luckily, nose cones are included amongst the 16,000 items held in the depot’s extensive stores.
Temple Mills also features a bogie drop that allows two trains to be worked on simultaneously as well as fully-automated wheel condition monitoring and re-profiling equipment.
“Wheel wear has been very much reduced since we’ve stopped running to Waterloo International and are no longer contracted to provide north of London sets for East Coast main line services,” said Peter.
“Also, money has been saved by removal of the now redundant third-rail shoegear and our on-site bogie repair facilities will soon cut out the need for road transport of components to France.”
Looking to the future, nearly 3,000 extra services a year will need to be run from 2012 to cater for 10 million passengers annually – up by one-fifth – and four new sidings will be needed at the depot.
“Our aspiration is to grow Temple Mills for even more centralised maintenance, and as a centre of excellence for all train experimentation and modification – a field in which we have already proved our expertise,” says David Bailey.
- Faithful shunter still has a place
With the demise of non-HS1 compatible Class 37 and 73 rescue locos – another Eurostar is now used for this purpose – the only conventional speed traction on depot is the faithful Class 08 diesel shunter, which is used for internal route learning as well as movement of Eurostars. Maintained under contract by EWS, the depot’s smoke detectors have to be de-activated whenever it works in the shed.
- Stop and think pink
The depot bikes used to speed engineers and transport small components are set to be replaced by a fleet of ladies’ models in garish pink. This is in a bid to halt any unaccountable losses of bikes, since nobody is likely to want to be seen riding a Lady Penelope version outside the depot!
- Staying clean and green
Temple Mills gives priority to ‘treading lightly’ in terms of environmental impact. The depot’s dedicated waste-handling centre sorts recycleable items, with waste such as oily rags going for incineration to generate power, maintaining a zero landfill
policy.
The carriage washer can re-use rinse water, and sensors throughout the offices switch off unwanted lights.
Also, good community relations are pursued with education and training partnerships with Newham and Waltham Forest colleges.
Reader Comments:
Views expressed in submitted comments are that of the author, and not necessarily shared by Railnews.
Jeremy, Chippenham, UK
I guess if you're the wife or girlfriend of someone at Temple Mills you can expect a bike for Christmas!